皮卡车架焊装生产线主要应用于皮卡车架分总成的拼装焊接,以及车架主体的机器人焊接。此项目包含36套工装夹具,配备了36台松下超低飞溅焊机和14台焊接机器人,使用的是日本进口的双脉冲松下焊机。该生产线应用了车架纵梁弧焊反变形技术、机器人自动焊接、车架自动输送和数字化工厂等技术,可实现多车型底盘的柔性化机器人自动焊接生产。
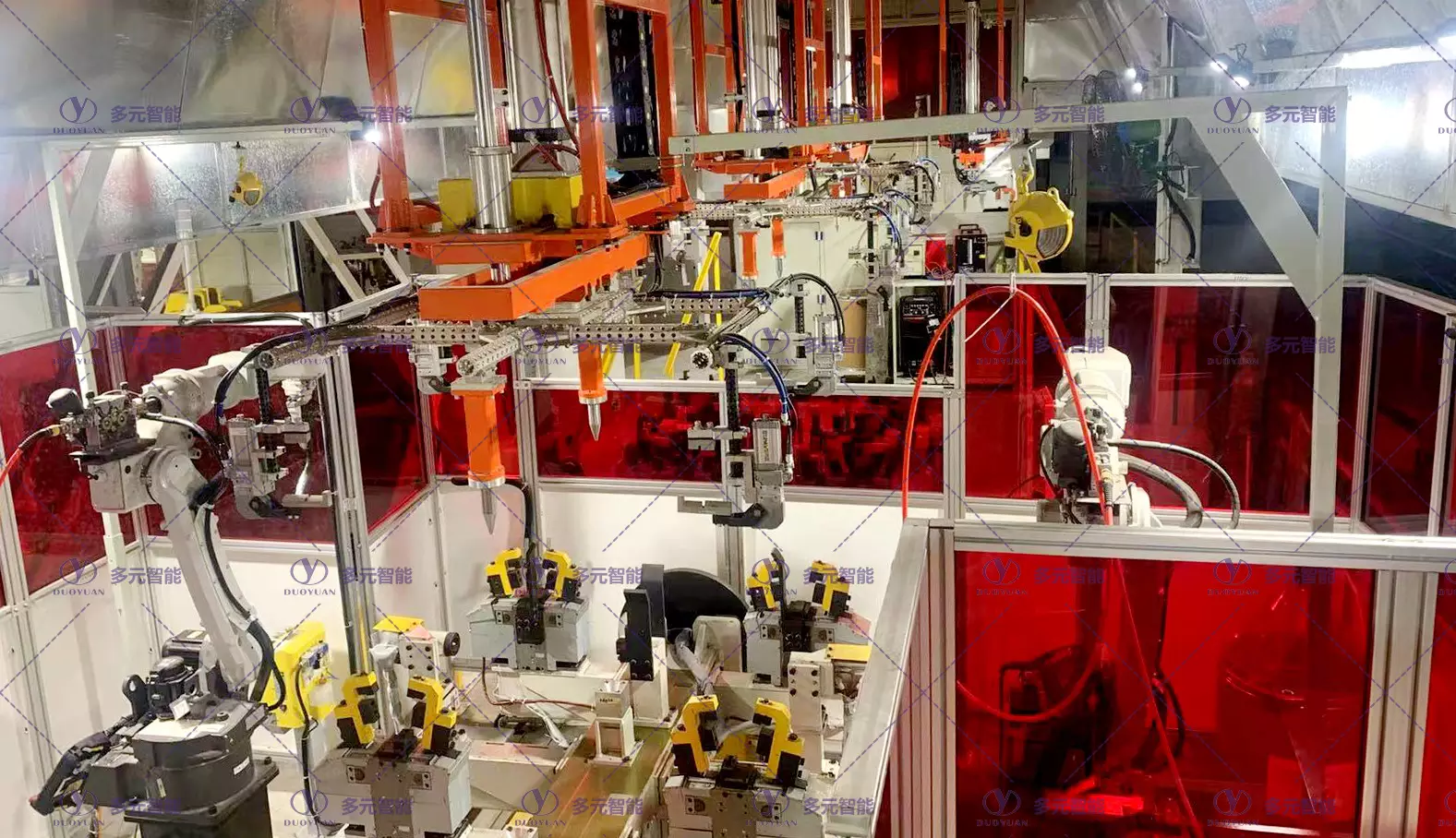
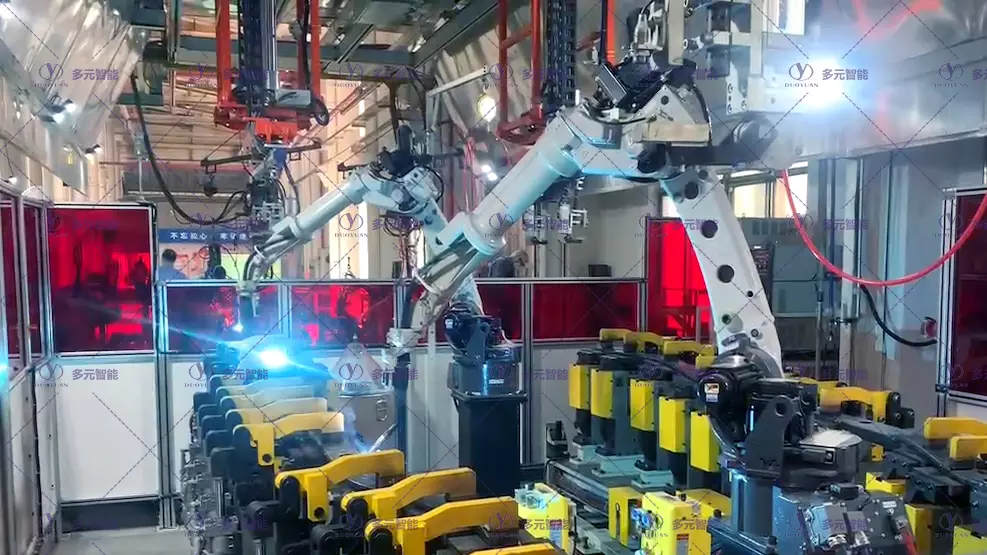
前车架和后车架的机器人焊接主要用于前后纵梁、横梁、纵梁中段和亏缩短拼装成前后车架主体的焊缝。前车架总成焊接分为四个工序:第一和第三工序为人工上件和点焊固定工位,第二和第四工序为机器人焊接工位(带变位机,确保每条焊缝都能焊到)。后车架总成焊接与前车架总成焊接相同,也划分为四个工位,可保证多车型共用。
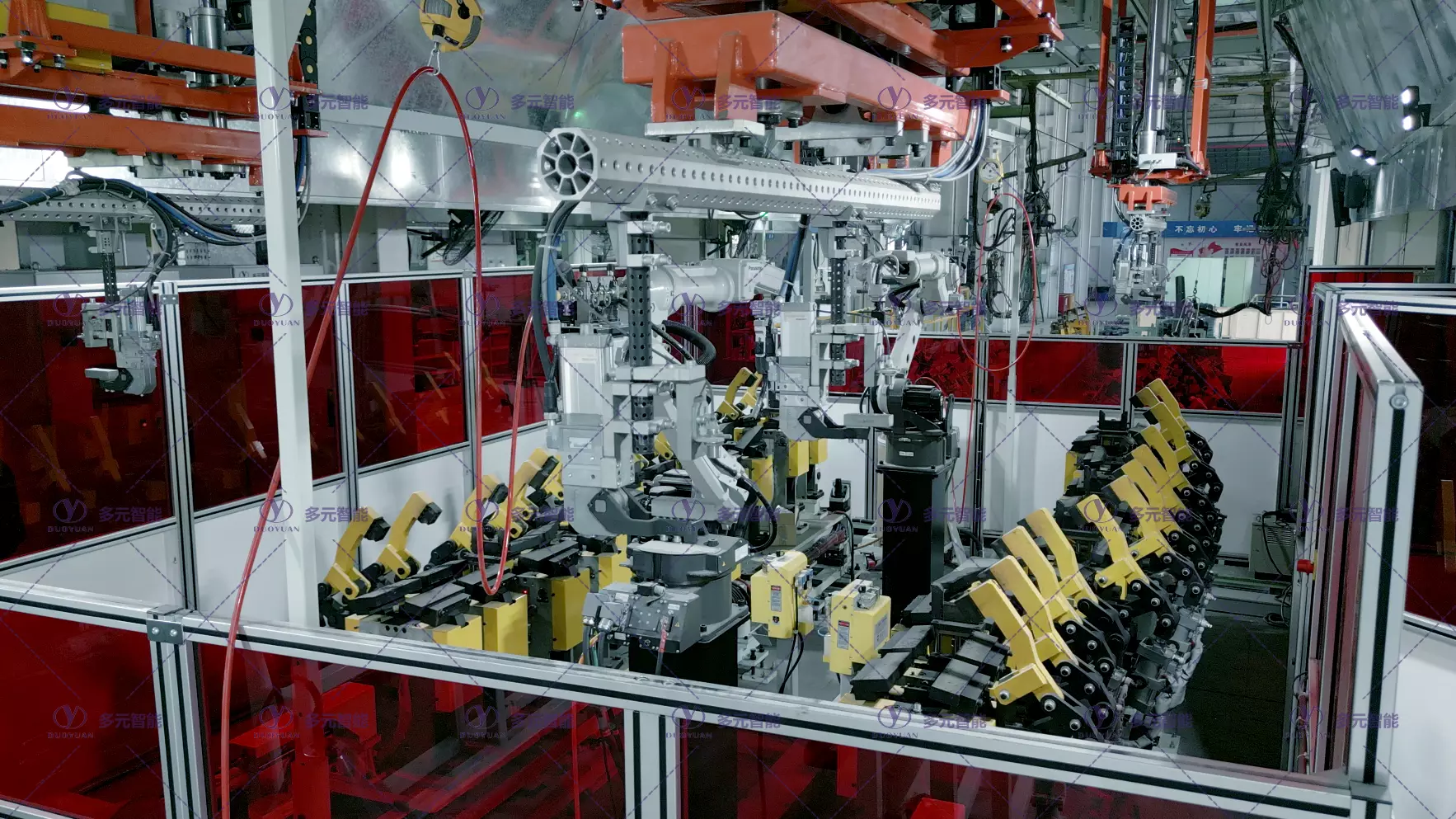
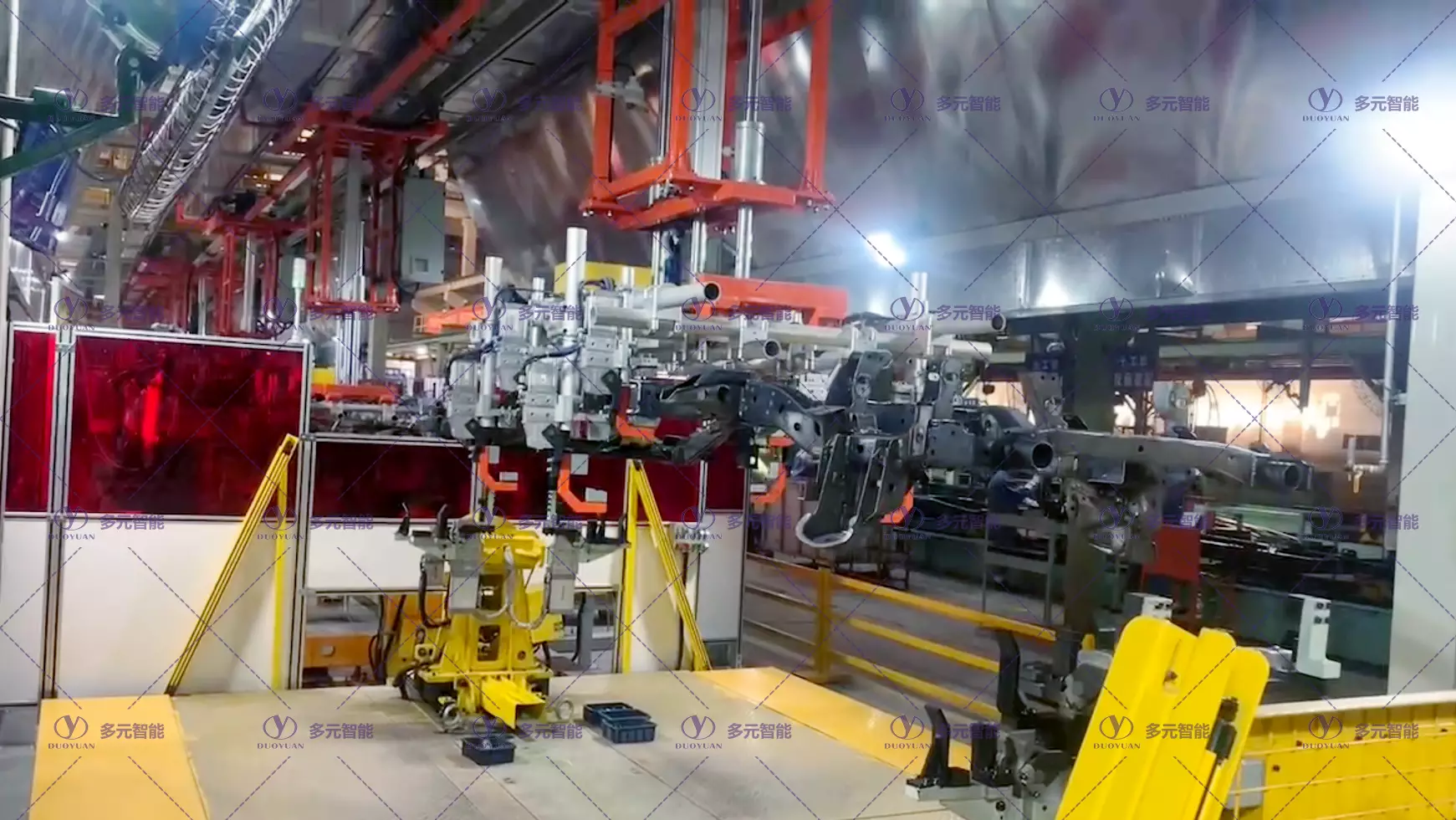
车架总成的机器人焊接主要用于将前车架和后车架拼装成车架总成的主体焊缝。人工补支架工位用于焊接车架精度要求最高的套管部件,进行补焊、打磨和人工检查修整,确保达到下线状态。
每个工位实现了自动化输送及工件的自动上料组合,输送驱动全部采用伺服电机控制,既能保证输送精度,也能满足特殊工况的使用需求。