H01新能源焊装线项目精心规划了主焊线与分拼线两大核心区域。从设计、生产到安装、调试,每一步都凝聚着我们对品质的极致追求。焊装线作为车身构造的基石,涵盖了主焊线、分拼线、调整线等线体,每一个环节都至关重要,共同构建起H01项目的坚固身躯。
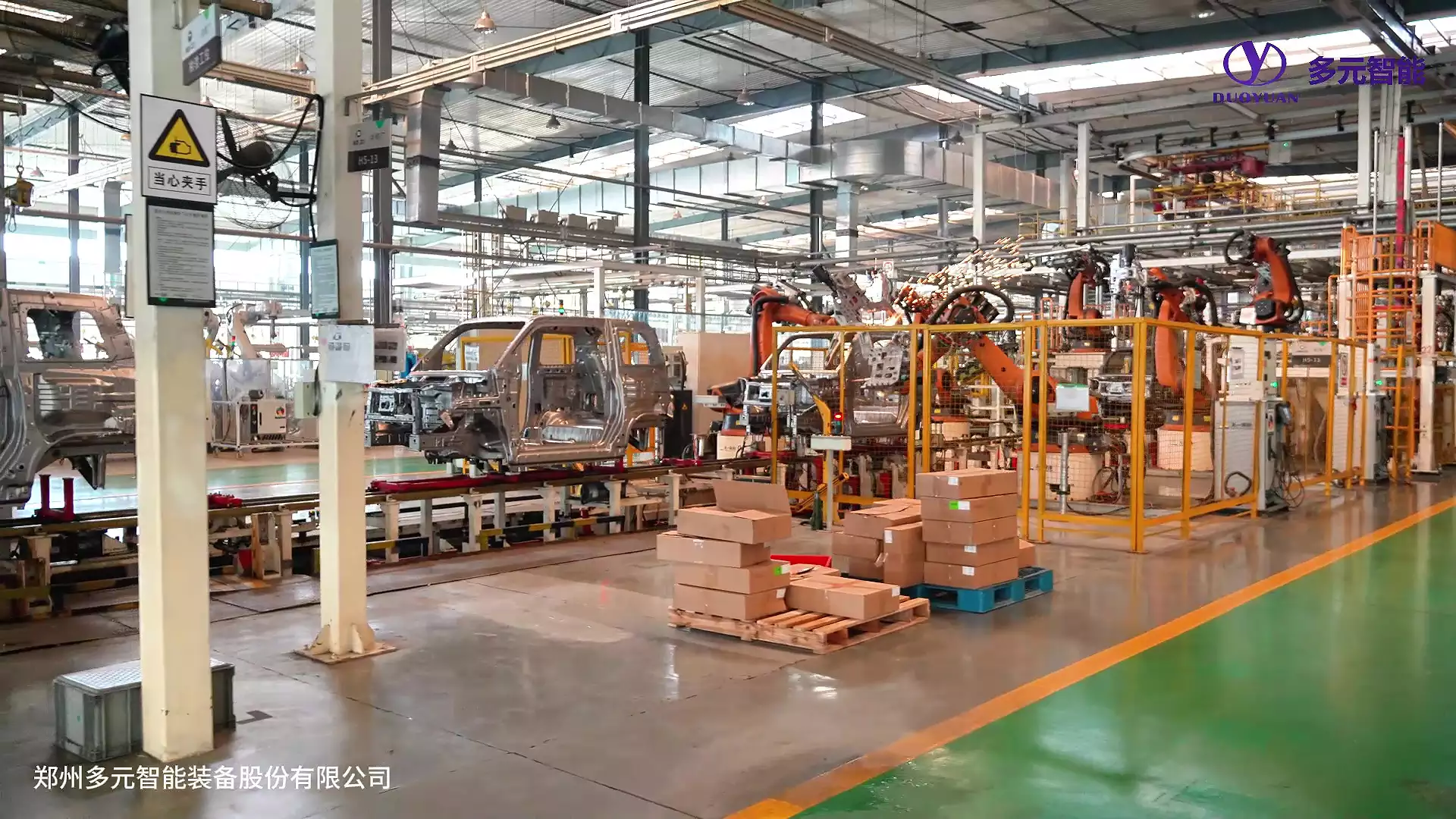
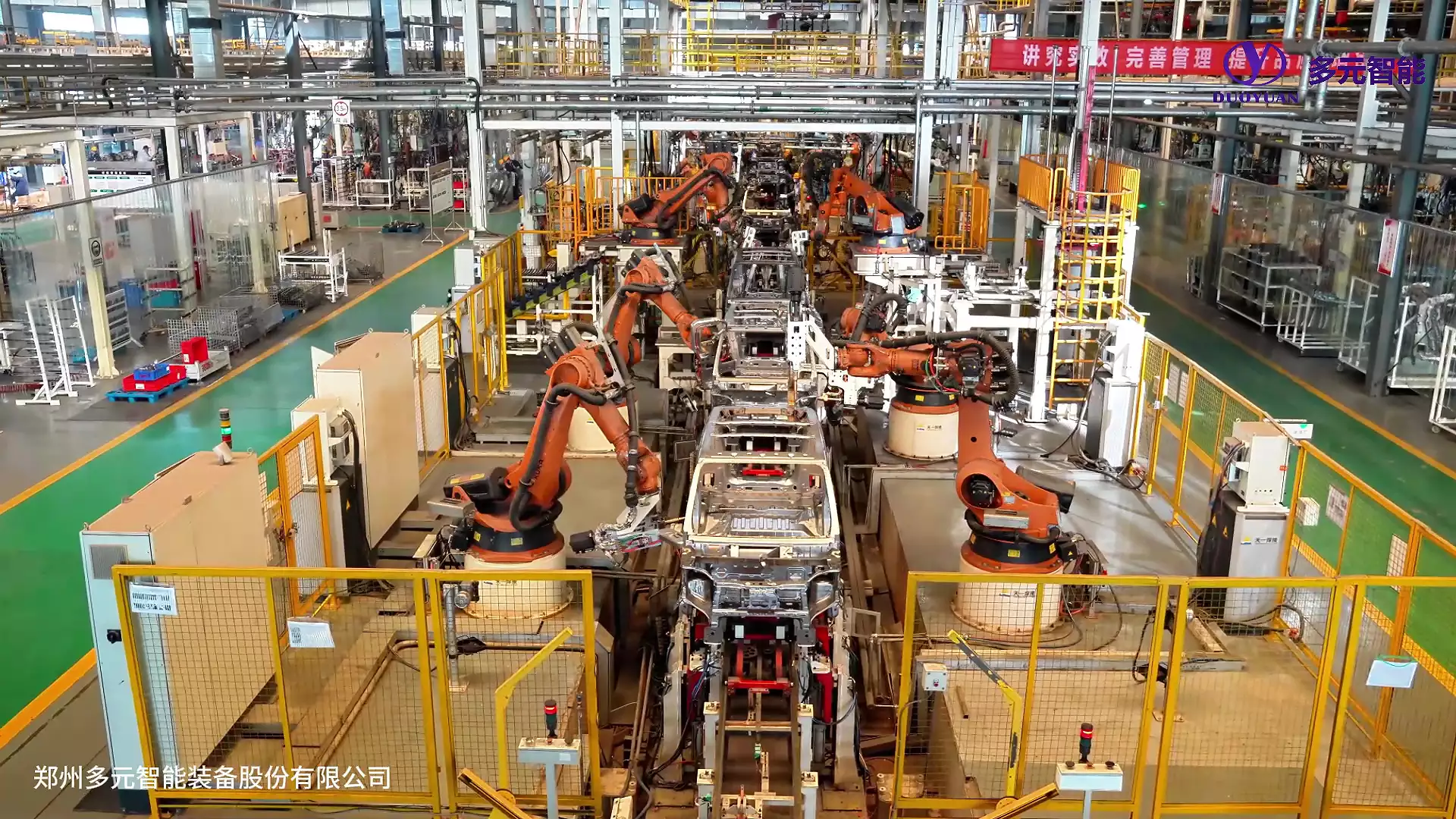
1. 高效输送系统
根据客户的产能和节拍需求,我们采用了FDS(柔性输送系统)、EMS(电动单轨系统)和AGV(自动导引车)相结合的输送方式,实现了物料的精准转运。
2. 模块化设计
模块化设计的巧妙运用使得车门、侧围、地板、机舱等各部件能够并行作业,实现了生产过程的连续性和高效性,赋予了分拼线高度的灵活性和可扩展性。无论是车型更迭还是产量调整,我们都能轻松应对,满足甲方的多样化需求。
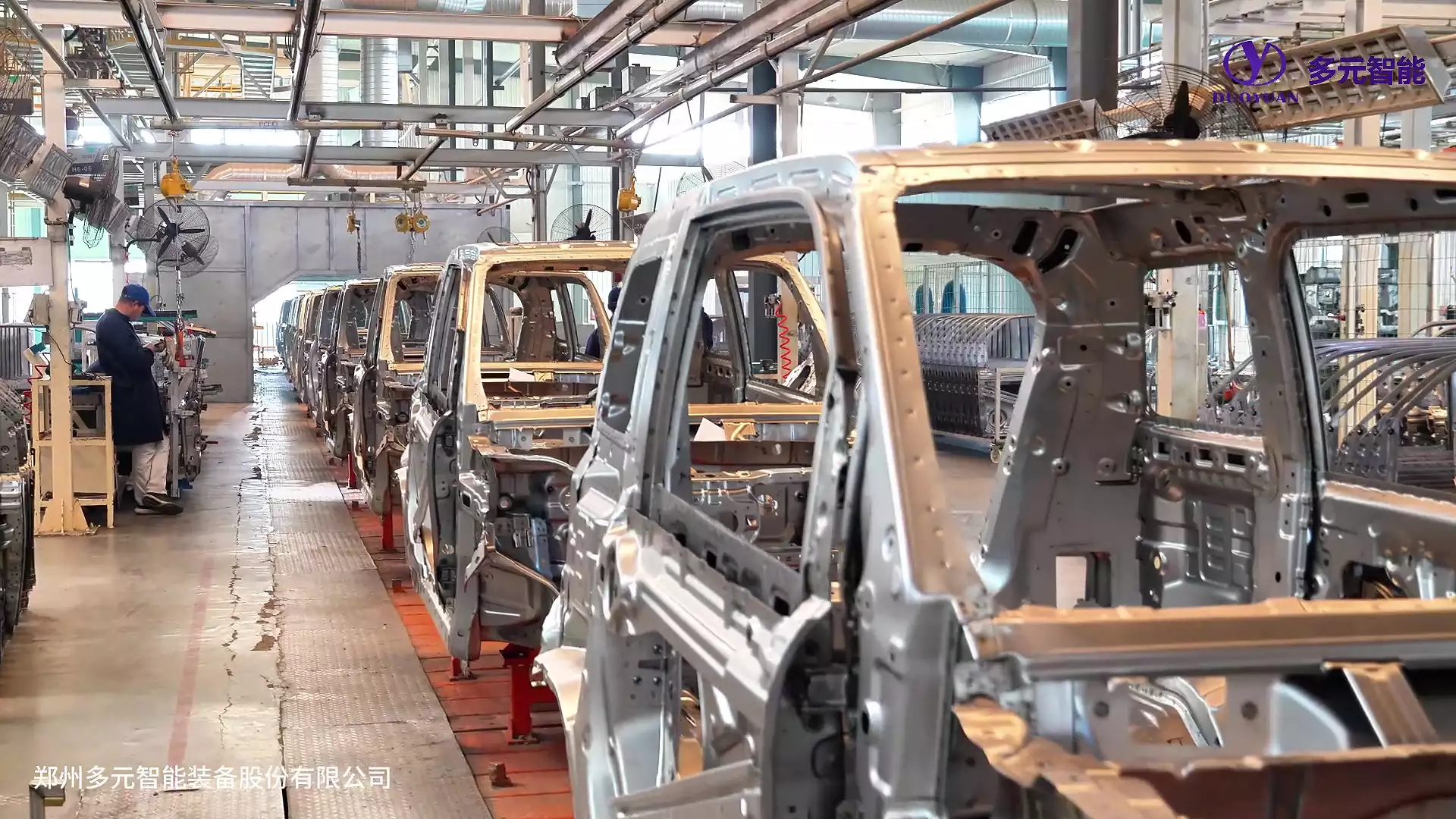
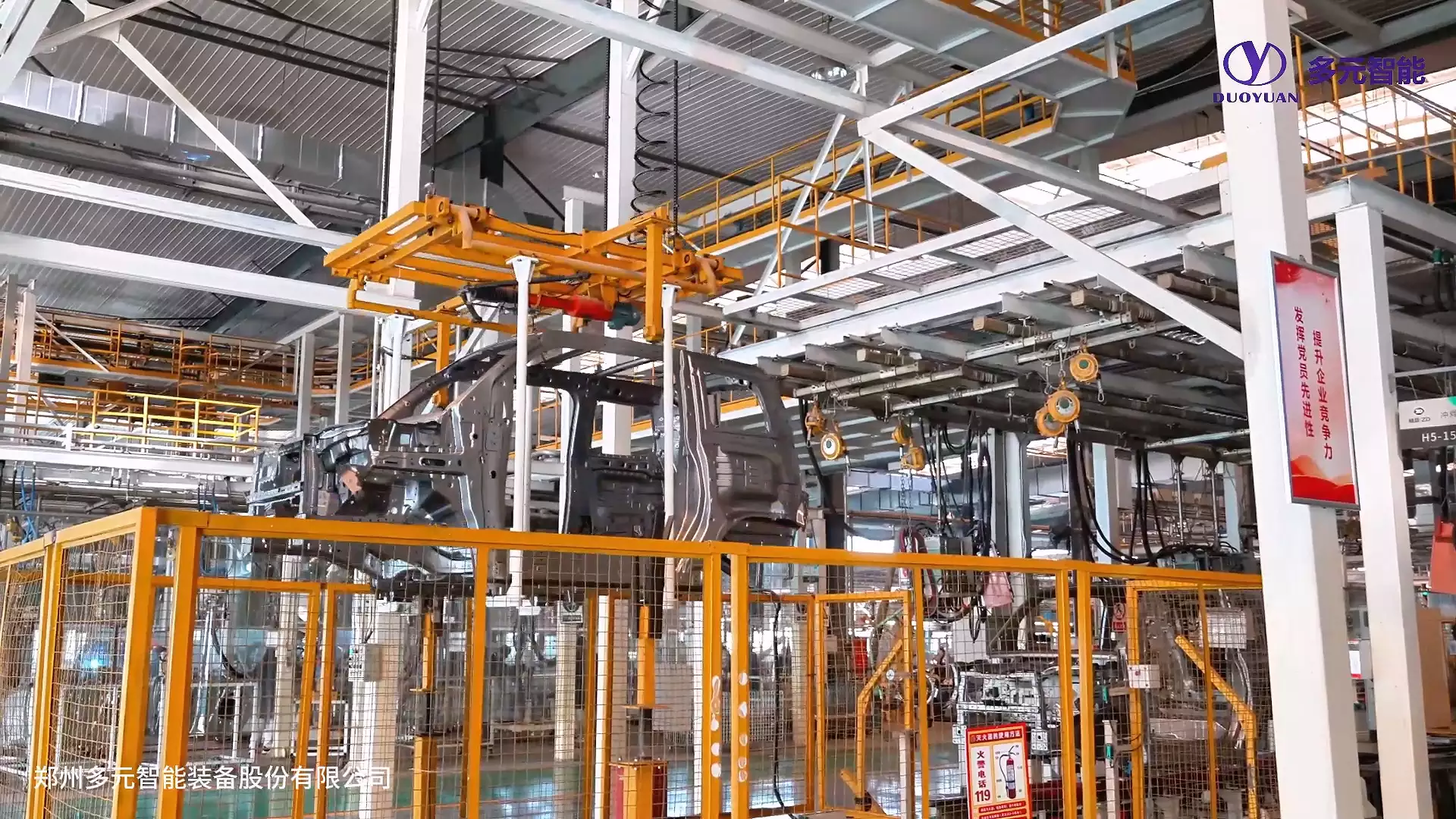
3. 机器人焊接技术
主焊线配备了15台高精度焊接机器人,实现了车身的全自动化焊接。前地板和机舱线的分总成通过AGV小车输送至主焊线上件工位,由机器人自动抓取上件进行焊接。在总拼工位中,左右侧围通过EMS输送落位,由2台抓取机器人和3台焊接机器人协同工作,确保了下车体、侧围及顶盖的精准焊接,并保障了高效的生产节奏。为了加强车身强度,在主焊线设置了人工补焊工位。完成的白车身框架通过EMS抓取输送至调整线,进行最终的车门安装和调整,确保每一台车的质量和安全性能。
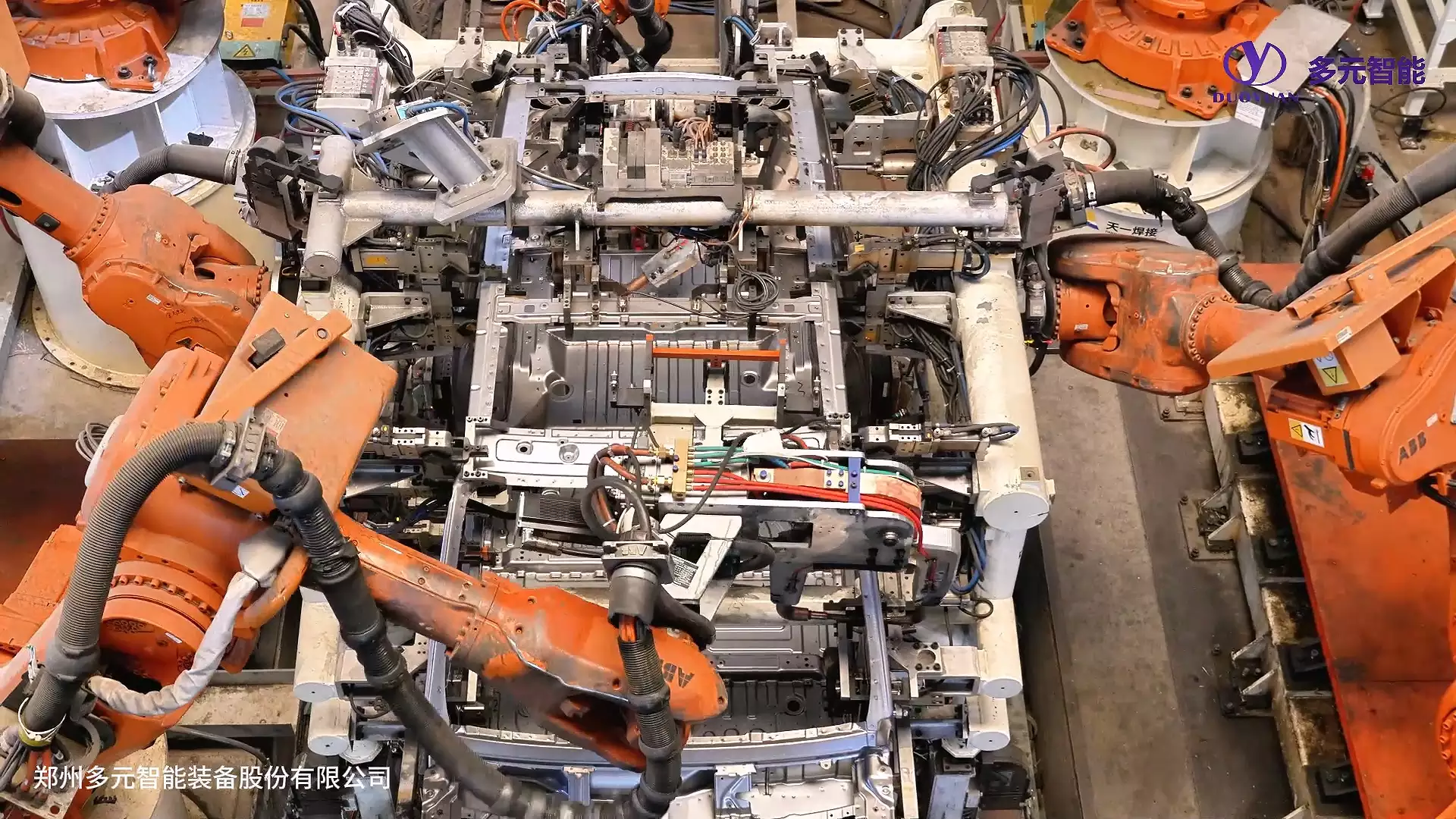
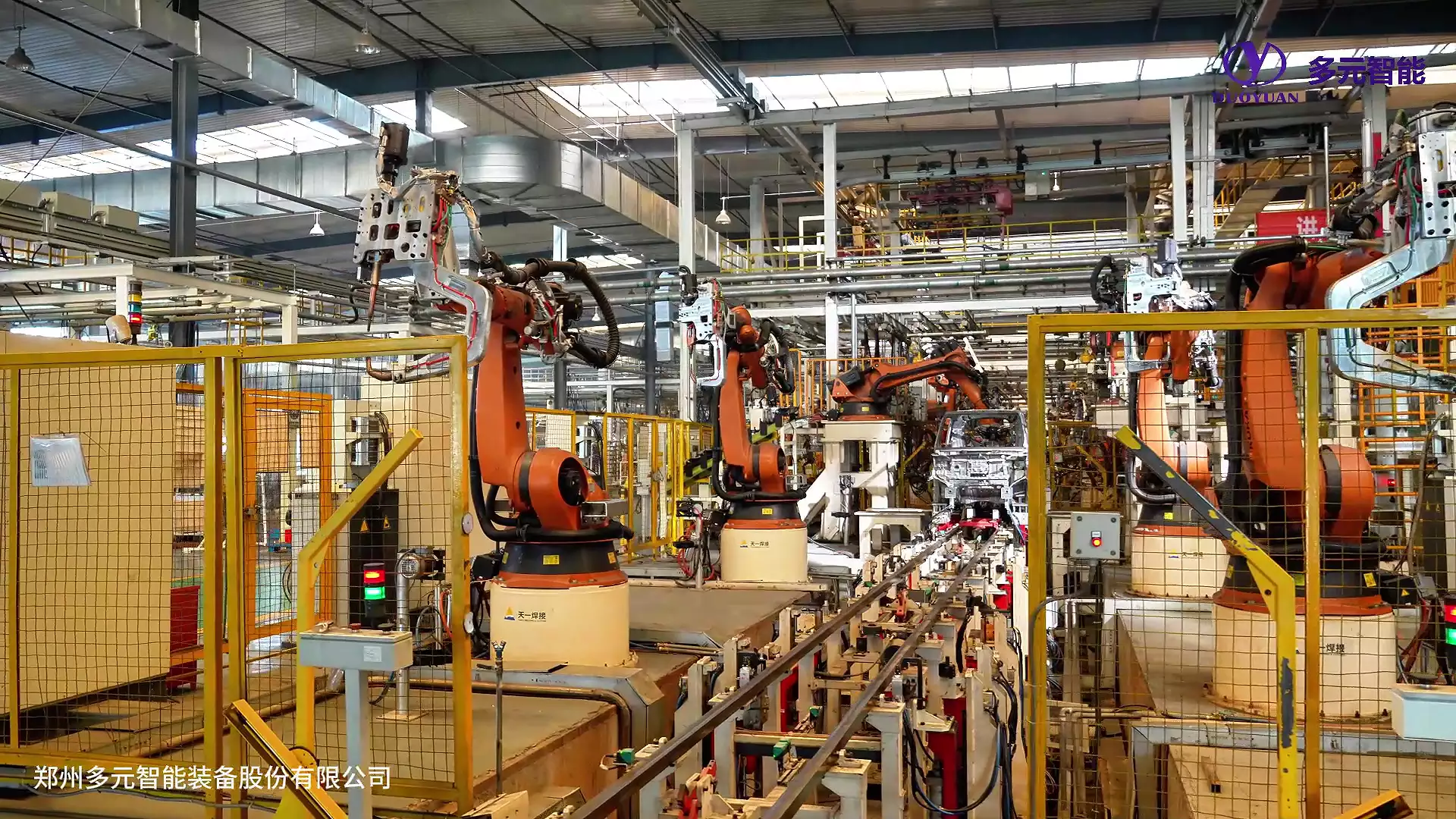
如今该项目已全面投产,设备精度、安全性能、可靠程度及生产节奏,均完美达标,为主机厂年产20万辆的宏伟蓝图奠定了坚实基础。